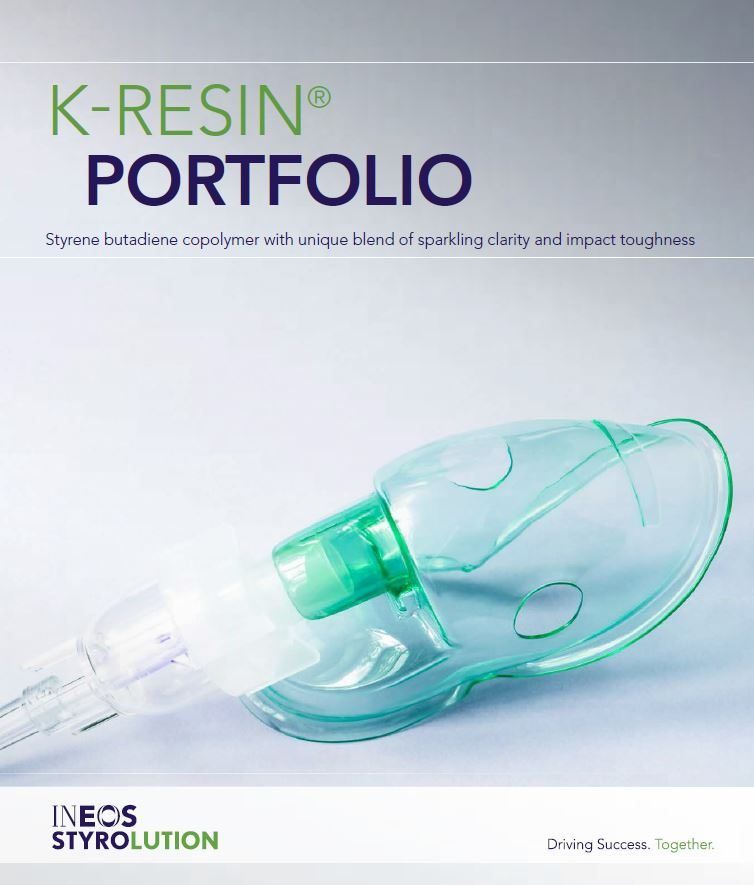
K-Resin®
Product Finder
Learn more about our new customer portal
Customer PortalAs a premier clear resin, K-Resin® SBC is known for its unique blend of sparkling clarity, impact toughness, stiffness and exceptional gloss. K-Resin® has been successively used for over 40 years in applications ranging from toys to packaging, from food containers to medical components, from consumer products to housewares and everything in between. It is often blended into crystal polystyrene to increase its impact and toughness without sacrificing clarity and transparency. It offers the excellent processability of styrenic resins and is suitable for all processing methods including injection molding, blow molding, cast and blown film, sheet extrusion and thermoforming. K-Resin®has good compatibility with many different polymers, therefore it is well suited for use in co-extrusion applications. K-Resin® can offer energy savings over other clear materials because it requires no drying prior to processing and because of the lower processing temperatures required.
While K-Resin® is most commonly blended with crystal polystyrene to increase stiffness and reduce cost, it can also be blended with several other polymers including SAN, PETG, PP and SMMA. Blending SAN into K-Resin can increase the stiffness and surface hardness while maintaining clarity. Blending with PETG can increase the impact strength while maintaining clarity. Blending with PP gives the molded part an interesting iridescent look. And blending with SMMA will result in increased stiffness, temperature resistance and surface hardness.
K-Resin® can be decorated using common methods such as hot stamping, screen printing, offset printing and flexographic printing. Grades of K-Resin® that contain mold release additives may require surface treatment before printing.