Polyolefin Foam Extrusion
Most commercial foam products can be classified as high-density foams or low-density foams. High-density foams have densities of 75% to 90% of the un-foamed polymer and are used in more permanent applications in furniture, cabinetry, material handling, industrial, construction, consumer, automotive, marine, and consumer markets. Low-density foams have densities of 10% to 20% of the un-foamed polymer. Low-density foams may be flexible or rigid, depending on the flexibility or rigidity of the base polymer. Flexible low-density foams are used for sound and heat barriers, for shock absorption, and for floatation applications. Rigid low-density foams are used for sanitary piping and conduit, pipe, and millwork. Polyolefins are ideally suited for the production of low-density extruded foams using physical or chemical foaming agents as they are capable of achieving very low density, resilient foams and can also be easily cross-linked. Common polyolefins used for extruded foam include LDPE, EVA, POE and OBC. HDPE, LLDPE and PP can also be foamed however, they can only produce high-density foams and are not capable of achieving the very low densities like LDPE, EVA, POE and OBC foams can.
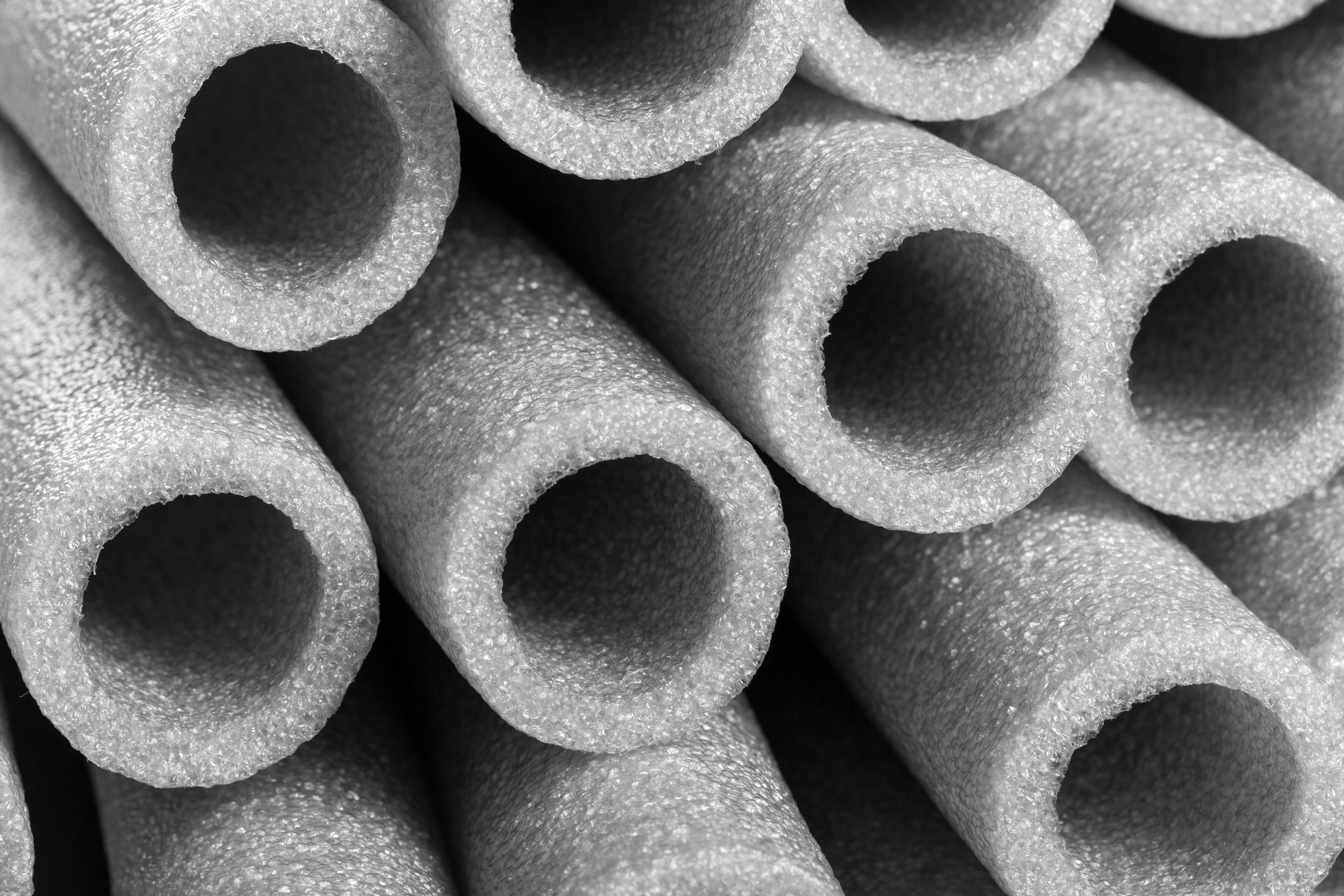
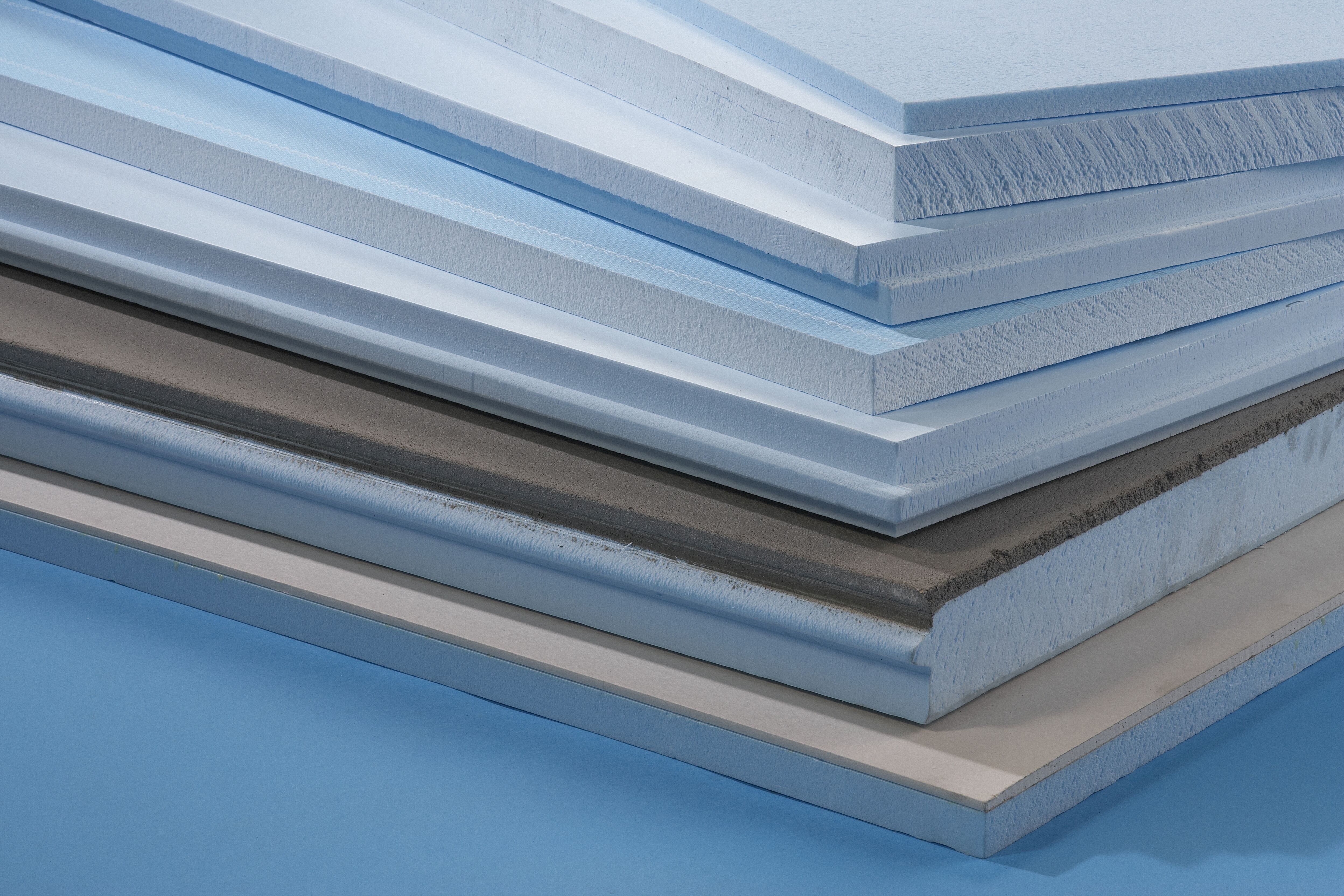
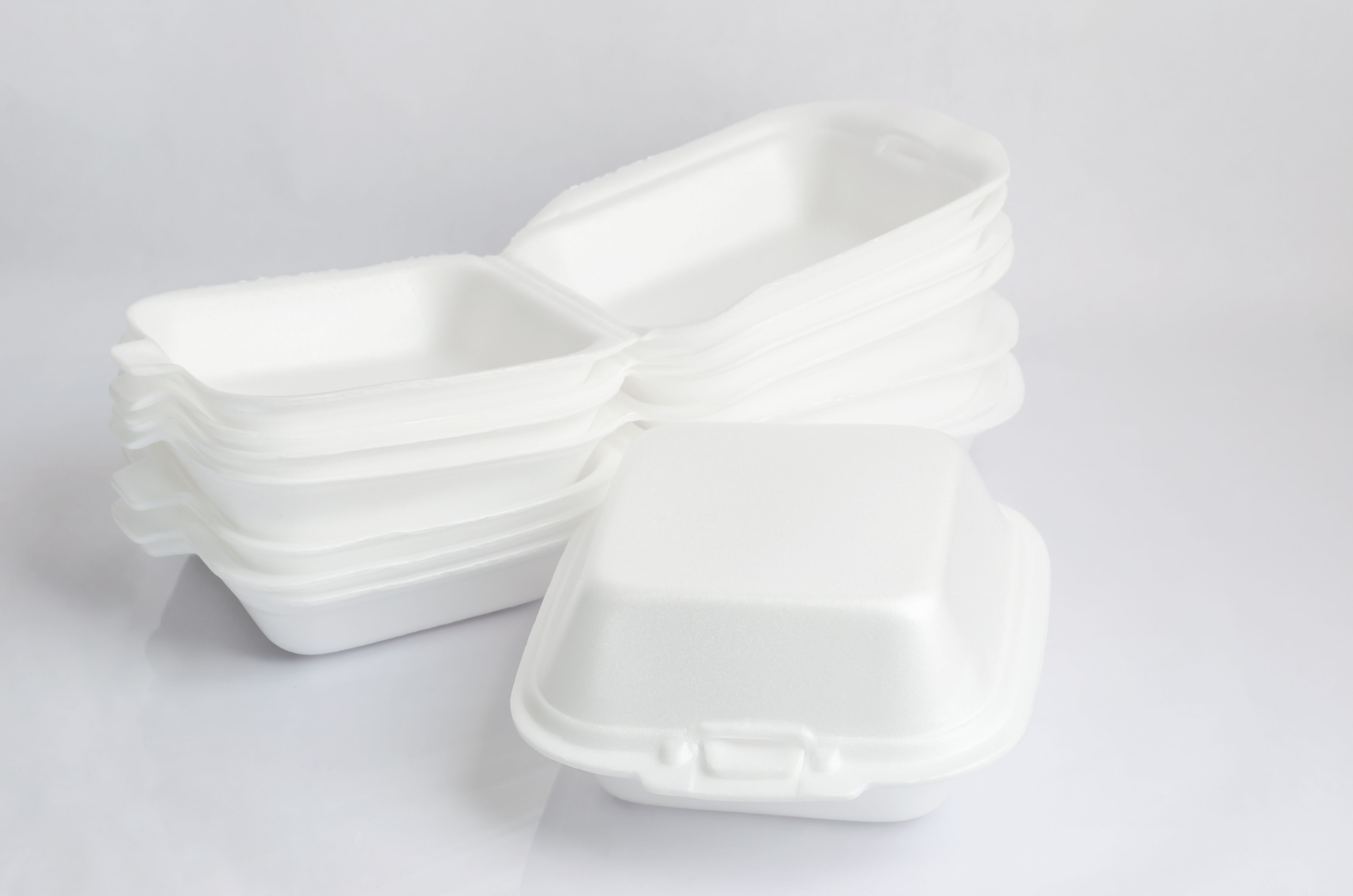
There are a few different technologies available for producing polyolefin foams by extrusion processing, but chemical foaming and physical foaming are the main foaming technologies. Chemical foaming involves the use of a chemical that reacts to produce gas through decomposition. Physical foaming agents can be either permanent or atmospheric gases or volatile liquids. Nitrogen and carbon dioxide are two common gases used to foam thermoplastics. These foaming gases must first be dissolved into the polymer to produce fine cells. Foam density depends on the amount of gas that is dissolved into the polymer, so its solubility in the polymer is especially important. Because nitrogen and carbon dioxide have limited solubility in most thermoplastics, they are not able to produce very low-density foam. Volatile liquids like butane and pentane, evaporate at the appropriate conditions to produce the foaming gas. These gases are relatively inexpensive and are easily transported and pumped into the extrusion equipment. They are, however, flammable, so care needs to be taken not only in their handling but in storing and handling the finished foam products.
The main ingredients in extruded polyolefin foam are the polymer itself and the foaming agent. Common polyolefins include LDPE, HDPE, EVA, polyethylene copolymers, and polypropylene, and the physical foaming agent is generally n-butane, iso-butane, n- pentane, iso-pentane, cyclopentane or a combination of these. Nucleating agents are fine particle size (1 to 20 microns) talc, calcium carbonate or another inorganic particulate and are generally added at 1% or less. The nucleating agent provides irregular surfaces, cracks, and crevices to which the dissolved gas molecules migrate and begin bubble growth. Cell stabilizers are required to stabilize the foam and to balance the outward migration of the foaming gas and the inward migration of air. The most common cell stabilizer is glycerol monostearate (GMS), but titanates have also been used. The typical loading level for cell stabilizers is 1% or less.
In order to produce high quality polyolefin foam, the foaming gas must be thoroughly dissolved and uniformly dispersed in the polymer melt. Bubbles start to form on the nucleating agent. Typically, the melt pressure in the extruder is high until just before the melt exits the die. As soon as the polymer melt exits the die, the pressure drops below the solubility pressure and microbubbles start to form on the nucleating agents. Once these microbubbles form, they grow rapidly, typically in less than 1 second, to a size of about 100 microns. For low density foam, the sheet or profile continues to expand freely after exiting the die. Free expansion of the foam yields very uniform, symmetrical cells with cell walls of uniform thickness.
Newly produced polyolefin foam may not be very dimensionally stable because as the foam cools, the internal cell gas pressure drops below atmospheric pressure. If the foam cannot support the pressure difference between atmospheric pressure and cell gas pressure, it will collapse or shrink. If air diffuses into the foam faster than the foaming gas can diffuse out, the foam may expand or grow. The polyolefin foam dimensions will eventually stabilize once the atmospheric pressure and cell gas pressure are equal. To help control and balance this outward and inward diffusion of foaming gas and air, cell stabilizers are incorporated into the foam formulation.
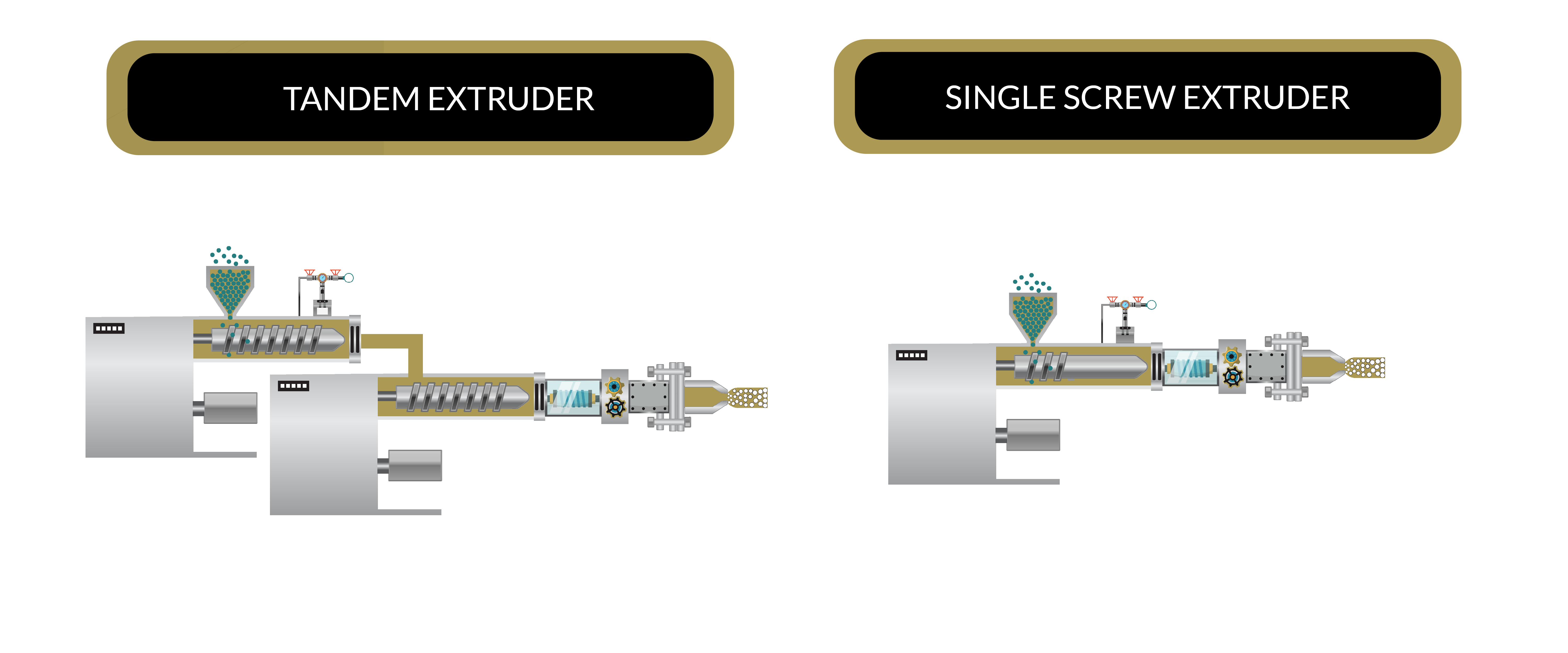
Extruder barrel temperatures for physical foaming of ethylene-based polyolefins are set to achieve a melt temperature of around 120°C. Too high of a melt temperature (greater than 145°C) often results in poor foaming and foam instability. Extruded polyolefin foam is often produced in the shape of a hollow tube, followed by slitting to produce a flat sheet. This sheet must then be cooled before rolling or cutting and stacking.
Download Now!