Injection Molding Troubleshooting Tips
Tip #4: Flash
Flash is a thin layer of plastic that flows outside of the cavity where the two halves of the injection mold meet. Over time flash can damage a mold so it is important to correct this molding fault as soon as possible.
Looking at possible causes of flash we can again separate them into material, machine/equipment and processing.
From a material standpoint typical causes of flash might be using a material with too high of a melt flow index or, in the case of nylon, processing the material with too high of a moisture content.
From a machine/equipment standpoint one should ensure that the mold is properly aligned and that the parting line is not damaged. Another possible area to check is to make sure the parting line of the mold does not have any contamination that could be preventing the mold from closing properly. A less common cause could be poor platen alignment. In some cases it may be necessary to change to a larger clamp tonnage machine.
From the processing side one should consider reducing the injection and/or hold pressure; increasing the clamp force; reducing the injection speed or lowering the melt temperature.
Entec Polymers Technical Service Team
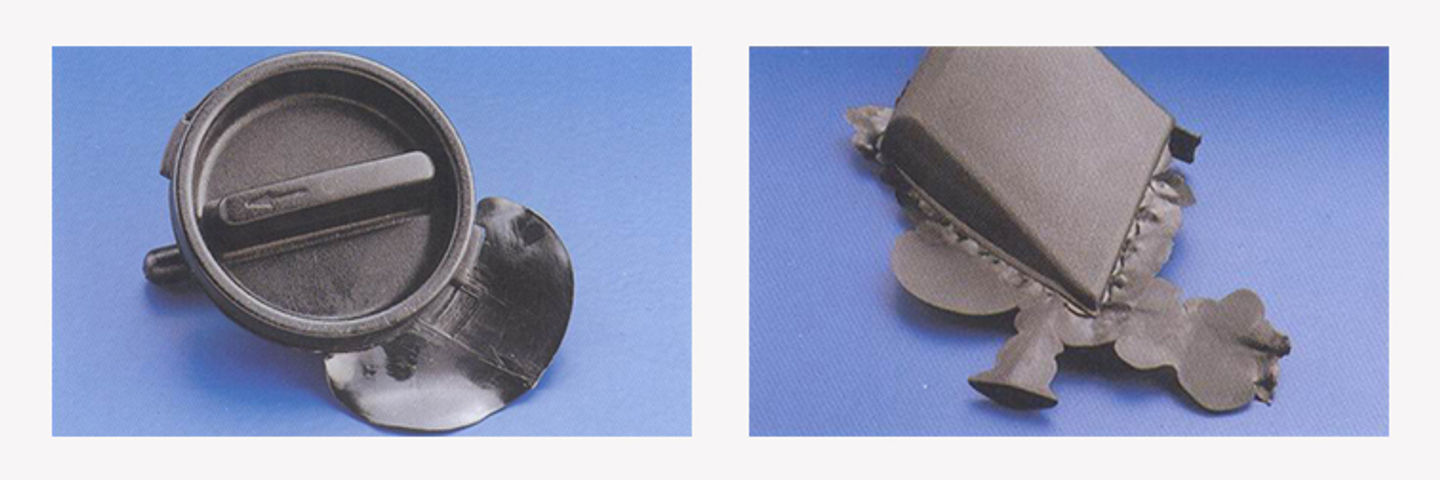