Abandoned fishing nets become high-performance motorcycle parts
Motorcycles give riders a sense of freedom and power, as well as the satisfaction that they look cool while cruising down the highway. But as bike OEMs continue to engineer new models with advanced performance and eye-catching appearance, there’s another priority impacting their design decisions today – environmental sustainability.
One iconic motorcycle manufacturer in the Midwest has partnered with NBP to develop sustainably-sourced electric bike parts made from an unexpected material – nylon fishing nets.
Parts made from ocean plastics are an increasingly popular request from OEMs that have company-wide sustainability initiatives.
“An electric bike already lends itself to lower carbon footprint because it eliminates harmful emissions, but it will have even lower total environmental impact if its parts are made from reclaimed materials that reduce waste in landfills,” says Joseph Mechery, Vice President of Sales at NBP.
Ensuring performance
The motorcycle OEM approached NBP to help find more sustainable options for the shrouding and other plastic components of its new electric bike.
The challenge was to find a polymer that could meet sustainability goals without compromising the company’s signature high-gloss appearance or superior performance. Many parts on the motorcycle need to be highly resistant to heat, strain, abrasion, and color fading. Also, the material needs to have all the right functionality for the injection molding process such as flow rate, cooling time, melt temperature, and viscosity.
NBP partnered with one of its resin distributors, Entec Polymers, and together they identified the option that met all those objectives –HYLON® Ocean nylon from Ravago Manufacturing. HYLON® Ocean compounds are based on recycled Nylon 6 (polyamide 6) pellets recovered from used fishing nets.
The news frequently shows video of plastic bottle waste floating in the ocean, but another major source of plastic pollution is abandoned nylon fish nets. In fact, the United Nations Environment Programme says, “Abandoned, lost and discarded fishing gear is the deadliest form of marine plastic, threatening 66 percent of marine animals and 50 percent of seabirds.”
Ocean preservation organizations harvest these “ghost nets.” Then they are cleaned and pelletized to become nylon feed stock used for injection molding. The result is a resin that performs identically to other Nylon 6 resins and even prime nylon in all properties, including density, flexibility, break stress, and heat deflection. Compared to prime nylon, the HYLON® Ocean has a similar price per pound and molds at the same cycle speeds, so the resin switch can be cost-neutral. To give the parts the greater stiffness/higher modulus, and other desired properties Entec blends the HYLON® Ocean resin with a glass fiber additive.
A wave of change
To date, the motorcycle OEM has piloted at least one of the new parts made by NBP and reports it has the same testing performance as its previous counterpart made with prime nylon. This project is the company’s first step toward adopting more sustainably sourced motorcycle parts, and many other automotive OEMs are asking about nylons from ocean plastics and bio-based plastics.
“Our customers are getting more and more knowledgeable by the day on recycled product offerings, which show that companies are looking to move towards more sustainable options, and they’re investing in it,” says Brandon Barker, business development at Ravago. “Any OEM with a sustainability platform using a high-performance material like nylon will find HYLON® is very suited to be a part of their material line.”
Learn more about how New Berlin Plastics can help you address sustainability goals with parts made from recycled plastics.
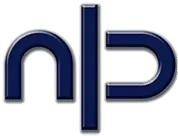
About New Berlin Plastics
New Berlin Plastics was founded in 1975 by William Aukofer and Robert Zeman. After two company moves in 1976 and 1982, business continued to expand, allowing NBP to transition to a new 100,000 square foot facility in 1998. This facility is located in New Berlin, Wisconsin and serves as the corporate headquarters and manufacturing site. In July of 2001, Jeffery Held and Mark Siewert acquired New Berlin Plastics. They worked together to grow the organization, focusing on both the day-to-day processes and the long-term goals.
New Berlin Plastics is more than an injection molder. We uphold business objectives that parallel the goals of your organization while providing you with superior manufacturing and comprehensive value-added services. The NBP team works alongside you on your project from the very beginning until your vision is achieved. We focus on delivering speed, accuracy, quality, cost-efficiency, competence, and value.