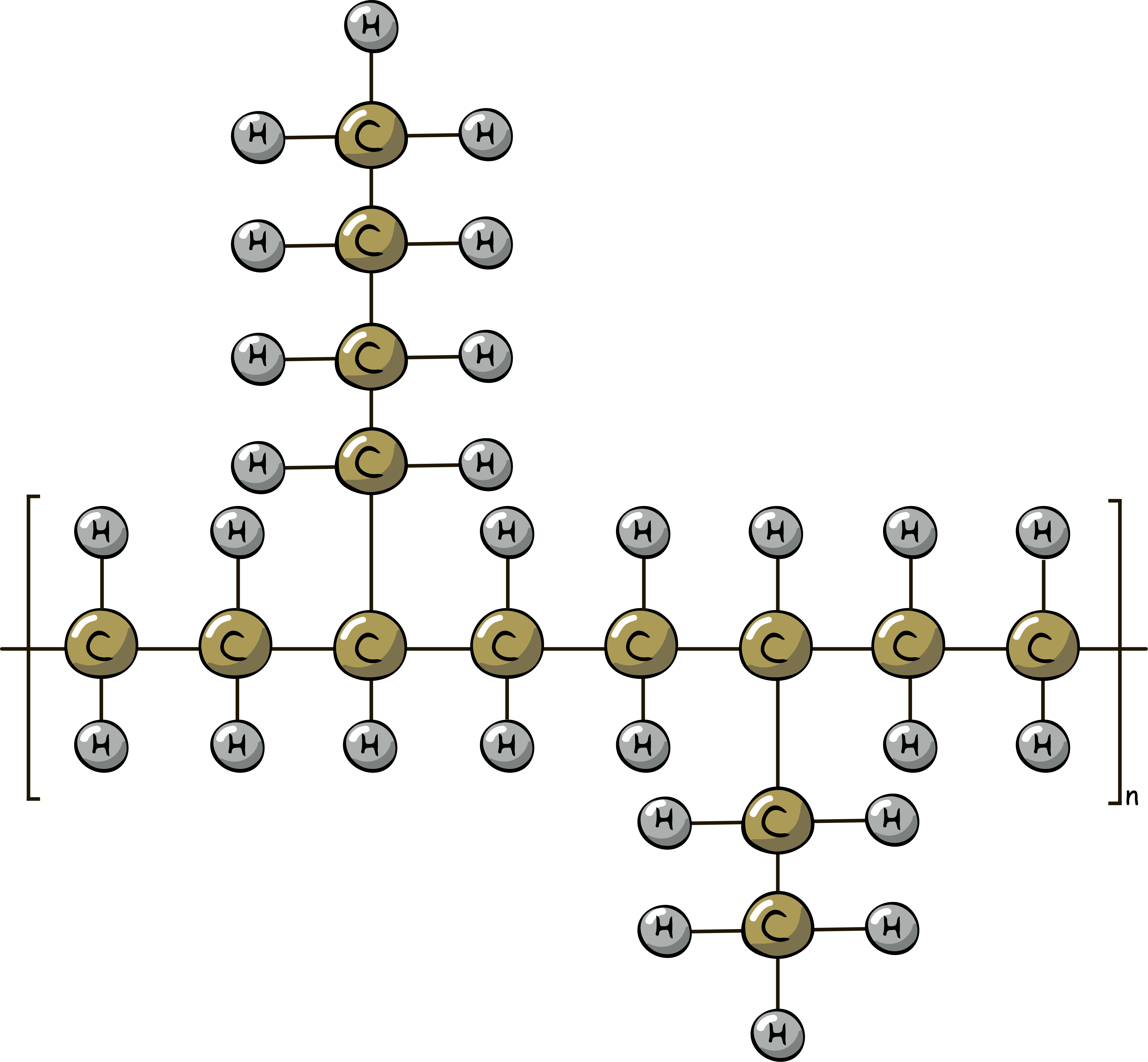
Low Density Polyethylene (LDPE) is produced in a high pressure autoclave or tubular reactor and is defined as having a density between 0.915 and 0.935 g/cm3. LDPE also has higher levels of long chain branching compared to other types of polyethylene. LDPE is known for its low density, high clarity, high flexibility and low stiffness. LDPE is very commonly processed by blown film and extrusion coating, although it is often injection molded as well. Common applications for LDPE include shrink film, collation film, extrusion coatings, caps, closures and lids, pharmaceutical bottles, wire and cable compounds, and foams.
Low Density Polyethylene (LDPE) is a widely used polymer known for its lower melting point and high flexibility making it ideal for film applications.
Polymer Characteristics
Low Density Polyethylene (LDPE) is a widely used thermoplastic polymer known for its unique characteristics that set it apart from other polyethylene grades. LDPE is characterized by a relatively low density and a highly branched molecular structure, giving it distinct physical properties. The branching in the polymer structure results in a less crystalline material, contributing to its flexibility and transparency.
One of the key features of LDPE is its excellent flexibility and toughness. This makes LDPE well-suited for applications where a pliable and impact-resistant material is essential. LDPE also exhibits good chemical resistance, making it suitable for various packaging applications where contact with different substances is common. However, this flexibility comes at the cost of lower tensile strength and a higher susceptibility to tearing compared to higher density polyethylene’s.
LDPE has a lower melting point compared to other polyethylene grades, making it ideal for multi-layer film applications. LDPE also has good melt strength that is advantageous in blown film processing. Additionally, LDPE is known for its transparency, which is valuable in applications where visibility or clarity is crucial.
Processing Methods
LDPE's unique characteristics make it highly amenable to a range of processing methods, providing versatility in the production of various products. Some common processing methods for LDPE include:
- Film and Sheet Extrusion: LDPE is widely used in the production of thin films and sheets, commonly employed in packaging applications. The material's flexibility, transparency, and ease of processing make it ideal for this purpose.
- Blow Molding: LDPE's excellent blow-molding characteristics make it suitable for the production of bottles, containers, and other hollow objects.
- Injection Molding: LDPE is used in injection molding for producing various products such as toys, lids, and containers where flexibility is prioritized over stiffness.
- Wire and Cable Insulation: LDPE's electrical insulating properties, combined with its flexibility, make it a suitable material for insulating wires and cables.
- Coating and Lamination: LDPE is often used as a coating or laminating material in the production of flexible packaging materials, providing moisture resistance and enhancing the durability of the final product.
The adaptability of LDPE to these diverse processing methods makes it a common material of choice in industries such as packaging, construction, and consumer goods.
Typical Applications
The properties of LDPE make it well-suited for a range of applications. Its flexibility and ease of processing make LDPE an ideal choice for packaging films, plastic bags, and containers. Additionally, LDPE is commonly used in the production of squeeze bottles, wire and cable insulation, and various molded consumer products. The versatility of LDPE allows it to fill niches where other polymers might be less suitable due to their different mechanical properties.
Molecular Structure
LDPE is characterized by its branched and more random molecular structure, which results in a lower density compared to High Density Polyethylene (HDPE). This structural arrangement contributes to LDPE's flexibility and ductility, making it suitable for applications requiring these properties.
Density and Mechanical Properties
The most apparent distinction lies in the density of LDPE, which is lower compared to HDPE. This lower density imparts LDPE with greater flexibility and a lower melting point. LDPE's mechanical properties, such as tensile strength and impact resistance, are affected by its branched structure, making it less rigid but more ductile than its higher density counterparts. This makes LDPE a preferred choice in applications where flexibility and impact resistance are crucial, such as in packaging and film production.
Thermal Properties
LDPE exhibits lower melting and softening points compared to higher density polymers. This characteristic makes LDPE suitable for applications that involve lower temperature processes, like blown film extrusion for packaging.