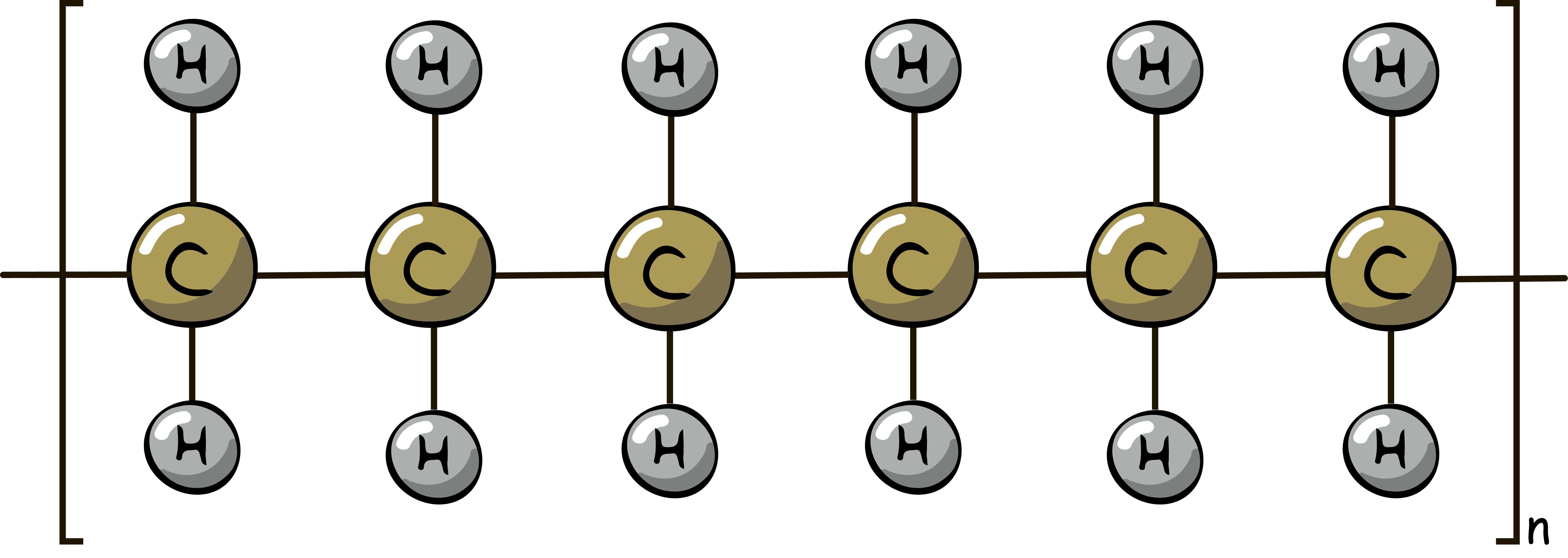
High Density Polyethylene (HDPE) is produced in low pressure reactors and has a very linear structure with few short chain branches. By definition, HDPE has a density greater than 0.940 g/cm3 and is the highest volume type of polyethylene in use today. Because of its high crystallinity, HDPE has high strength, stiffness and hardness, high temperature resistance, and excellent chemical resistance, although very high crystallinity grades can suffer from poor environmental stress crack resistance. HDPE is processed by injection molding, blow molding, sheet and profile extrusion and film extrusion. Common applications for HDPE include buckets, pails, crates, pallets, film, bottles, automotive components and wire and cable compounds.
High Density Polyethylene (HDPE) is a widely used polymer with distinctive characteristics like chemical resistance, abrasion, impact and mechanical properties, that set it apart from other polymers.
Polymer Characteristics
High Density Polyethylene (HDPE) is a versatile thermoplastic polymer known for its high strength, durability, and chemical resistance. The key characteristic defining HDPE is its high density, achieved through a linear polymer chain with minimal branching. This results in a tightly packed, crystalline structure, contributing to its excellent mechanical properties. HDPE exhibits a high tensile strength, impact resistance, and stiffness, making it suitable for a broad range of applications. Additionally, HDPE is inert to many chemicals, rendering it resistant to corrosion and a broad range of chemicals. Its high melting point and excellent thermal stability further enhance its utility in applications at elevated temperatures.
Processing Methods
HDPE's versatility extends to its processability, with a variety of methods employed in its fabrication. Common processing methods include:
- Injection Molding: Used for manufacturing complex-shaped parts such as crates, trash cans, caps, and automotive components.
- Blow Molding: Ideal for producing hollow objects like bottles, tanks, and industrial containers.
- Extrusion: A processing method used in the production of pipes, films, and sheets. In profile extrusion, HDPE can be shaped into various profiles for a wide range of applications.
- Rotational Molding: Suitable for large, hollow items like tanks, containers, and playground equipment.
- Compression Molding: Applied in the production of large, low-volume parts like automotive components and recreational equipment.
The choice of processing method depends on factors such as the intended application, product geometry, and required mechanical properties. HDPE's ease of processing contributes to its widespread adoption in diverse industries, offering manufacturers flexibility in producing a range of products.
Typical Applications
- Crates
- Bottles
- Playground Equipment
- Trash Cans
- Kayaks
- Containers
- Pipe
- Tubing
- Sheet
- Bags
- Flexible Packaging
- Medical Components
Molecular Structure
One of the primary distinctions lies in the molecular structure of HDPE compared to other polymers. HDPE is a linear polymer with a high degree of crystallinity, resulting in a tightly packed structure. This molecular arrangement contributes to its high tensile strength and excellent chemical resistance. In contrast, other polymers like Low-Density Polyethylene (LDPE) and Polypropylene (PP) have different molecular structures, leading to differences in properties such as flexibility and melting point.
Density and Strength
As the name suggests, HDPE is characterized by its high density, which significantly impacts its strength and durability. The tight packing of chains in HDPE contributes to its impressive properties. This makes HDPE ideal for applications requiring robust materials, such as in the manufacturing of pipes, containers, and packaging. Other polymers like LDPE, with a lower density, exhibit lower strength but possess increased flexibility, making them suitable for applications requiring higher flexibility.
Thermal Properties
HDPE exhibits excellent thermal properties compared to other types of polyethylene, including a high melting point and resistance to heat deformation. These characteristics make HDPE a preferred choice in applications requiring high thermal stability.
Chemical Resistance
HDPE is renowned for its exceptional chemical resistance, making it resistant to a wide range of chemicals, acids, and solvents. This property is crucial in applications where the material comes into contact with various substances, such as in the chemical industry and packaging of aggressive substances. While other polymers may also possess chemical resistance, the specific nature of HDPE's molecular structure contributes to its superior resistance to many chemicals.
Environmental Impact
In recent years, environmental considerations have become increasingly important in material selection. HDPE stands out in this regard due to its recyclability and relatively low environmental impact. The ease of recycling HDPE contributes to its sustainability, making it a preferred choice in various industries seeking environmentally friendly solutions.