Injection Molding Troubleshooting Tips
Tip #3: Burn Marks
Burn marks, or dieseling, is the scorching or blackening of material at the end of the flow. This is caused by compression and super-heating of the air on front of the melt flow front. Besides the black appearance on the molded part, dieseling can cause damage to the mold itself.
When looking for the cause of burn marks / dieseling, one can look at the effects of material, equipment and processing set up. From a material standpoint you may want to ensure that the material is not over-dried which could affect the flow and filling characteristics. You may also want to determine if the material is an incorrect melt flow rate and whether a higher flowing material should be used.
From an equipment standpoint the main item to check is mold venting. You should ensure that the mold has sufficient venting and that the vents are not plugged.
From a processing standpoint you want to ensure that the material is being processed at the correct melt temperature. Over-heating the material can cause out-gassing which can contribute to poor venting (plugging) of the mold. Injection speed should also be evaluated and reduced if necessary. Back-pressure on the screw should be evaluated as well, and reduced if excessive.
Entec Polymers Technical Service Team
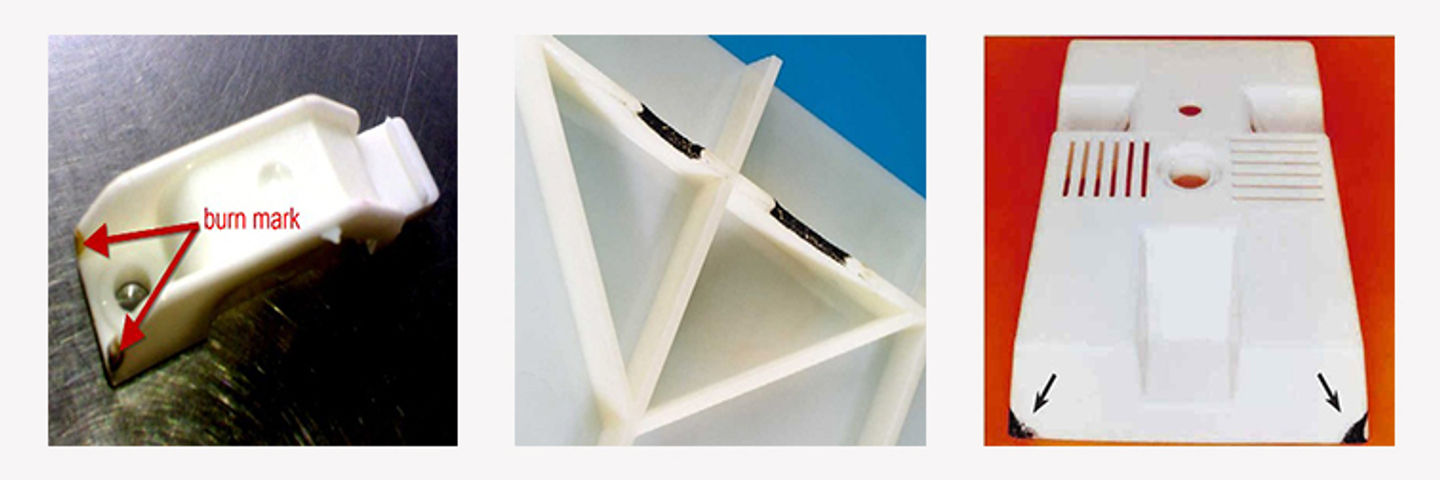